Perfekt samspill mellom AGV-er og manuelle trucker
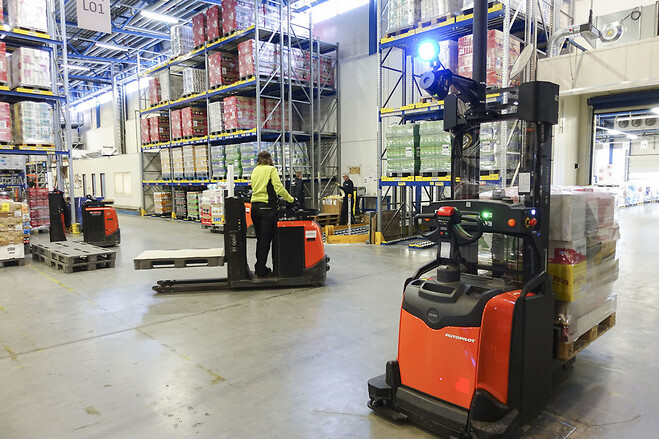
På flere lagre i Europa finner man autotrucker som er blitt parkert for godt fordi brukeren aldri klarte å løse utfordringene med å få autotruckene til å fungere i et blandet miljø. I Trondheim kom man raskt over dette stadiet.
Roger Tømmervold, ansvarlig for eiendom og intern logistikk i Coop Norge Trondheim, legger ikke skjul på at det var en tanke kaotisk også hos dem rett etter at de fem AGV-ene ble tatt i bruk i oktober i fjor. På lageret finnes det totalt over 210 trucker som kjøres i et svært hektisk miljø og i starten syntes truckførerne det var litt skummelt å måtte forholde seg til roboter som kjørte av seg selv. Ikke fikk de blikkontakt med dem heller for å bli enige om hvordan de skulle kjøre, slik de slik de var vant med overfor de andre truckførerne. Resultatet var at de dels kjørte for nærme AGV-ene slik at de stoppet, at de stod litt i veien for hverandre eller ventet unødvendig lenge på å få klar bane.
På flere lagre i Europa finner man autotrucker som støver ned i et hjørne der de er blitt parkert for godt fordi brukeren aldri klarte å løse utfordringene med å få autotruckene til å fungere i et slikt blandet miljø. I Trondheim kom man raskt over dette stadiet. Tømmervold forteller at truckførerne for lengst har lært seg kjøremønsteret til AGV-ene og hvordan de ter seg. Resultatet er at AGV-ene uhindret kan kjøre sine faste ruter midt i en sverm av manuelle trucker som passerer dem både på «innern» og «yttern» uten at det av den grunn går på sikkerheten løs.
Kartla 17.500 potensielle AGV-transporter
Coop er den nest største dagligvareaktøren i Norge med en markedsandel i fjor på i underkant av 30 prosent. I tillegg til sentrallageret (CLog) på Gardermoen har Coop regionlagre i Stavanger, Bergen, Trondheim og Tromsø.
Lageret i Trondheim er på rundt 30.000 kvm og etterforsyner i overkant av 300 butikker fra Nordfjordeid og Oppdal i sør til Bodø i nord.
Gjennomsnittlig per dag kommer det ca. 2.500 paller inn, ca. 65.000 kolli blir plukket og ca. 3.500 paller sendes ut. Frukt/grønt og frys produseres i sin helhet i Trondheim, mens resten er en miks med ferdigproduserte paller fra CLog som bare cross-stockes før de går videre ut til butikk.
Tømmervold forteller at de for tre år siden begynte å vurdere mulighetene for å automatisere interntransporten.
– Vi ønsket å se på alle muligheter og gikk bredt ut uten noen begrensninger. Det endte med at vi fant frem til at hele 17.500 rene A- til B-transporter i uken som ville kunne automatiseres. For ikke å gripe over for mye på en gang komprimerte vi dette ned til rundt 3.000 til 3.500 transporter som vi ønsket å prøve ut, forteller han.
Etter at Coop lokalt i Trondheim hadde fått tegnet grovskissen for hva som var mulig å få til og utarbeidet et business-case med en payback ca. to år, ble dette meldt inn til avdelingen for sentral logistikkutvikling der Hege Sandanger ble satt på som prosjektleder og overtok ansvaret for den videre fremdriften.
Imponerende grundig forarbeid
Selv om Coop har rammeavtaler med flere leverandører av konvensjonelle trucker er de aller fleste på lageret i Trondheim blitt levert av Toyota Material Handling Norway (TMHNO) som også har sitt hovedkontor i Trondheim.
– I den innledende fasen snakket vi kun med dem, men det var bare for å finne ut hva som var mulig og hva som ikke var mulig og foregikk helt uten forpliktelser. Da det etter hvert ble besluttet at vi skulle gå videre og investere i autotrucker gikk vi ut med en tilbudsinnbydelse. Av de syv som svarte på prekvalifiseringen valgte vi å gå videre med fire, forteller Tømmervold. Han legger til at det var en svært omfattende prosess og at Toyota på ingen måte ble begunstiget eller hadde noen fordeler.
– Vi endte likevel opp med dem fordi de etter vår mening rett og slett kunne tilby den beste leveransen, konkluderer han.
Karim El-Kelish, Logistic Solutions Manager i TMHNO, er mektig imponert av forarbeidet til Coop. For å lykkes med et AGV-prosjekt poengterer han at det er helt avgjørende at brukeren utfører en like grundig jobb som det Tømmervold gjorde i forkant med både å kartlegge alle mulige transporter og så brekke det ned til hva som er reelt.
– Etter det regnet vi på kapasiteter og forsøkte å estimere hvor mange AGV-er de måtte ha for å kunne løse oppdragene, men det var ikke tilstrekkelig for Roger, som deretter gikk etter oss i sømmene gjennom å kjøre snile med stoppeklokke og i samme hastighet som en AGV for å kontrollere at våre beregninger var riktige. For oss var det veldig godt å få en bekreftelse på at vi opererte med reelle tall, sier El-Kelish.
– Og fra vår side var det viktig å få bekreftet at Toyota ikke lovet mer enn de kunne holde da vi bygget opp business-caset, tillegger Tømmervold med et smil.
Tung systemutvikling
Foruten å få skaffe midler til selve AGV-anskaffelsen var det minst like viktig for Hege Sandanger å sikre tilstrekkelige it-ressurser til prosjektet.
– Vi har gjort svært mye på systemsiden og som har vært helt avgjørende for prosjektet. En AGV er jo helt avhengig av å bli styrt av et system, og et slikt hadde vi rett og slett ikke, forteller Tømmervold. Han legger til at de ikke ville gå til anskaffelse av noe nytt wms og i stedet utvide funksjonaliteten i selskapets SAP slik at når AGV-en kjører gjennom scannerportalen og spør SAP hvor den skal kjøre så får den et svar.
Det er ikke mer avansert kommunikasjon enn det, men å få programmert inn alt dette var ifølge Sandanger og Tømmervold en temmelig omfattende jobb. Likevel ga det gevinster langt utover bare det å kunne styre AGV-ene.
– For utgående varer hadde vi tidligere en statisk løsning der de enkelte butikkene hadde sine faste tildelte felt. Nå har vi i stedet valgt å satse på dynamiske feltløsninger slik at det kunne bli en logikk rundt hvordan det skulle tilbakemeldes. Avhengig av mengde blir feltene nå beregnet fra gang til gang og det bidrar også til en bedre tilpasning av bilene, sier Sandanger.
– Er det riktig det som hevdes at det aldri har vært mer orden og struktur her på lageret enn nå?
– Ja, vi har nok beveget oss fra en litt kaotisk verden hvor vi produserte nærmest i alle kriker og kroker og det var ikke fullt før det rant over, sier Tømmervold. – Nå har vi fått en veldig god systemstøtte på vareflyten, inkludert et helt annet forhold til kapasiteter her på huset enn hva vi hadde tidligere. Takket være det har vi kunnet endre utlastprofilen for å redusere belastningen på området. Tidligere hadde vi peaker som lå over kapasiteten, men nå har vi fått en langt flatere utlastingsprofil gjennom uken. Det var en viktig forutsetning for å kunne lykkes med AGV-prosjektet,
Flere ulike transportoppdrag med AGV
Ved hjelp av Toyotas grafiske grensesnittet C-Way har Tømmervold fra PC-en sin full kontroll over hvor AGV-ene til enhver tid befinner seg på lageret.
– Du kan jo gjette hva som er det første jeg kontrollerer når jeg sitter med kaffekoppen lørdag morgen. Hvis jeg ser at AGV-ene står uvirksomme må jeg ta en telefon og spørre. Nei da, så ille er det selvfølgelig ikke, men herfra har jeg full kontroll, sier han og peker på skjermen som viser et oversiktsbilde over lagerlayouten hvor alle AGV-kjørebanene er tegnet inn og posisjonen til AGV-ene vises i sanntid.
– Primæroppgaven er å transportere de rundt 3.000 ferdigproduserte pallene i uken vi får fra CLog som AGV-ene plukker opp på varemottaket, gjennom en scannerportal og videre til utlastfelt. Hvis det ikke er ledig der kjører de opp på mellomlagringsområde et stykke unna. På den måten får vi de pallene som ikke er klare likevel inn i et system med en gang, forklarer Tømmervold. Han opplyser at de også har et eget tilleggsområde for det som skal ut i løpet av helgen fordi det da må mellomlagres mer enn normalt.
– Det er veldig viktig å sikre at AGV-ene har nok å kjøre, og siden pallene fra CLog kommer litt i rykk og napp, har vi koblet på noen pri 2-oppdrag. Det dreier seg om transport av både våre ferdigproduserte kjølevarer og kald frukt og grønt som kjøres gjennom en annen scannerportal og ut til utlastfelt. I tillegg har vi tegnet inn ytterligere ett område som skal håndtere CLog kjøl, men den kjøres fortatt manuelt. Som et pri 3-oppdrag har vi tegnet inn en stasjon for tompaller og søppel opp mot returstasjon som ligger 180 meter unna.
På spørsmål om hvordan man styrer AGV-ene mellom de ulike oppgavene, opplyser El-Kelish at det kan skje automatisk, men at Coop bevisst har valgt en løsning med manuell oppstart av oppdrag. Det utføres på skjermen ved å trykke på knapper for ferdigdefinerte oppgaver. Da skifter samtidig AGV-kjørebanene farge på skjermen slik at man svært lett ser hvilke jobber som er aktivert.
Medarbeiderne tok eierskap
Hvordan reagerte så medarbeiderne på sine nye robotkollegaer?
Tømmervold forteller at da de ble informert om hva som skulle skje, var den første tanken til svært mange at nå biter de over for mye og at det måtte være umulig å blande inn AGV-er i den intense driften på lageret. Enkelte førere av dobbelsniler hadde dessuten store problemer med å forstå effektiviteten til en AGV siden de jo selv kjørte to paller dobbelt så fort som AGV-ene.
– Da de begynte å komme på plass kom selvfølgelig spørsmålet om hvordan dette ville påvirke den enkeltes arbeidsoppgaver. Vi engasjerte naturligvis verneapparat, tillitsvalgte og hele systemet fra dag én.
Tømmervold forteller at de tidlig i prosjektet ansatte to AGV-operatører. I tillegg til de to spesialistene gikk de også svært bredt ut med opplæring hvor målet var at alle skulle kunne håndtere AGV-ene i det daglige og tildele dem oppdrag.
– På den måten fikk de ansatte et eierskap til dem og da opplevde vi at stemningen skiftet litt. I dag opplever vi at AGV-ene har blitt akseptert som et verktøy.
Han legger til at AGV-ene ikke har resultert i noen nedbemanning av den faste arbeidsstokken, men kun medført mindre bruk av innleid arbeidskraft for å ta topper.
Fortsatt fintuning
Både Tømmervold og El-Kelish forteller om enkelte mindre hendelser i startfasen som har resultert i skader som måtte repareres.
– Dette har dels vært forårsaket av brukerfeil eller fordi systemet ikke var optimalt. Anlegget er fortsatt ikke overtatt formelt av Coop og vi fintuner fortsatt, sier El-Kelish, som legger til at de både har opplevd at en AGV har blitt påkjørt av en manuell truck og vice versa.
– Men er det mulig med alle sensorene som AGV-en er utstyrt med?
– Ja, og det skyldes at de først og fremst er utstyrt med et «Personal Protect System» og ikke et antikollisjonssystem. Ett eksempel på det er at sensoren i kjøreretningen ikke klarte å fange opp gaflene til en konvensjonell truck som stakk ut kjørebanen til AGV-en. Plasseringen 10,5 cm over gulvet var i henhold til både direktiv og normer, men er nå blitt senket.
En annen utfordring med å mikse AGV-er og manuelle trucker så tett som Coop i Trondheim har gjort det, er at ståplattformen på de manuelle truckene er i en slik høyde at de hverken blir detektert av sensoren eller kan bli truffet av de mekaniske gaffeltuppsensorene. Det har resultert i et par påkjørsler bakfra i dropfeltene, og for å bedre deteksjonen og unngå dette videre har man enkelt og greit bare sveiset på noen korte kjettingstumper som henger ned fra ståplattformene.
Tømmervold synes TMHNO har vært kreative og raskt løst utfordringene som har dukket opp.
– Mye av det som har oppstått skyldes dessuten at driften vår er litt spesiell og ikke svakheter på AGV-en.
Kjører fra kl. 5 til kl. 22
På Coop-lageret i Trondheim jobber ca. 235 årsverk med plukk og transport av paller. Det foregår fra klokken 6 til kl. 20 (18 på fredag). I tillegg er en liten styrke på plass én time tidligere for å ta imot varer, mens en utlaster og en driftsoperatør arbeider frem til kl. 22 på kvelden. En betydelig styrke jobber også på lørdag for å gjøre klar det som skal ut på søndag og mandag.
– Hvor lenge går AGV-ene da?
– Det er ønskelig at de skal tas i bruk allerede kl. 5 og kjøres helt til klokken 22, men samtidig forventer jeg ikke mer enn 9,5 timer driftstid i det tidsrommet, sier Tømmervold.
Selv om Toyotas autotrucker kan leveres med litium-ion-batterier som vil klare to skift med litt klattlading, valgte Coop konvensjonelle 500 Ah bly-/styrebatterier og batteribytte.
– Vi ville ikke at AGV-ene skulle stå på lading og valgte i stedet en «formel 1-løsning» hvor de kjører inn for et raskt pitstop og batteribytte.
Og raskt går det virkelig. Hege Sandanger forteller at de en gang fikk en advarsel fordi de hadde byttet for raskt. Det skjedde på under to minutter og da klarte ikke systemet å forstå hva som faktisk hadde skjedd.
Ønsker å automatisere mer
Lageret i Trondheim har så mange Toyotatrucker i drift at TMHNO har et verksted med egne teknikere på stedet, tilsvarende halvannet årsverk. Autopilot, som AGV-ene benevnes, er bygget på standardtrucker og de faste teknikerne kan derfor hjelpe til med det tekniske. I tillegg har TMHNO sentralt spesialister på den autonome biten som enten feilsøker via VPN eller rykker ut til kundene ved behov.
AGV-prosjektet i Trondheim er det første og så langt det eneste automatiseringsprosjektet som Coop har gjennomført – selvfølgelig utenom sentrallageret CLog som til gjengjeld er tilnærmet fullautomatisert. Hege Sandanger opplyser at avdelingen for sentral logistikkutvikling heller ikke arbeider med noen andre konkrete AGV-prosjekter, men at flere i ledelsen utviser stor interesse for AGV-er.
– Men i Trondheim har Roger Tømmervold ønskene klare, i første omgang å utvide med flere AGV-er på utlast.
– På gode uker kjører de 2.700 paller og vi begynner derfor å nærme oss målet vi har satt på mellom 3.000 og 3.500 paller i uken. Selv om vi har en del halvpaller og andre ukurante lastbærere som AGV-ene kan få problemer med, har vi likevel veldig mye mer som kan kjøres med slike.
– Er det fristende å trekke inn AGV i plukk også?
– Da vi jobbet med business-caset for tre år siden så vi både på å mate blokker med en skyvemast-AGV og på langsniler som kunne droppe fra varemottak og ut i områder til skyvemast. Men ett sted måtte vi begynne og da var det naturlig å gå for de store og lange transportene først.
Likevel var Tømmervold svært bevisst på at AGV-ene skulle ha tilstrekkelig løftehøyde for å kunne levere i både andre og tredje høyde i blokk.
– Det var rett og slett for ikke å låse seg helt til det vi skulle begynne med og dermed ha muligheten til å kunne sette dem inn i annet arbeid dersom det blir noen fremtidige endringer. Av samme grunn gikk vi også en del opp i løftekapasitet slik at vi også har muligheter til å kunne løfte tyngre enn de gjør i dag hvis det blir aktuelt. Tenk flerbruk – det er kjempesmart, avslutter Roger Tømmervold.
BT Staxio Autopilot
Ifølge TMHNO vil et komplett autotrucksystem normalt bli tjent inn i løpet av ett til tre år og rundt 75 prosent av dem har en inntjeningsperiode på ca. to år. |
Coop NorgeCoop Norge har seks matvarekjeder og fire non-foodkjeder som i fjor hadde en samlet omsetning på 48 milliarder kroner. Innenfor dagligvare er selskapet den nest største aktøren i Norge med en markedsandel i fjor på 29,7 prosent. I tillegg til det fullautomatiserte sentrallageret (CLog) på Gardermoen finnes det regionlagre i Stavanger, Bergen, Trondheim og Tromsø. Totalt leveres det til nærmere 1.200 dagligvarebutikker og det plukkes 120 millioner kolli i året. Over 60 prosent av volumet automatplukkes på CLog. Lageret til Coop Norge Trondheim ligger på Tiller og etterforsyner i overkant av 300 butikker fra Nordfjordeid og Oppdal i sør til Bodø i nord. Det er på rundt 30.000 kvm og er delt inn i varemottak, frukt og grønt, fryseavdeling, kjøleavdeling, tørrvareavdeling, utlastområde (med 49 porter) og en gjenbruksstasjon. Frukt, grønt og frys produseres i sin helhet i Trondheim, mens resten er en miks med ferdigproduserte paller fra CLog som cross-stockes før de går videre ut til butikk. Lageret 3.500 plukkplasser og 12.500 bufferplasser. Gjennomsnittlig per dag kommer det ca. 2.500 paller inn, ca. 65.000 kolli blir plukket og ca. 3.500 paller sendes ut. Uteområdet har god plass til 50 vogntog og ukentlig er rundt 700 lastebiler innom lageret. |
Opphav og kilder: Logistikk & Ledelse nr. 1-2019