Pallegrossisten: Har tatt Industri 4.0 til Dale
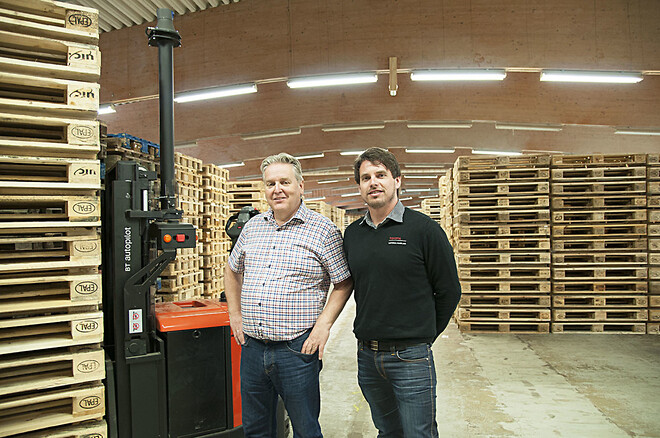
Dale ligger omtrent midtveis mellom Bergen og Voss og er et typisk vestlandsk industritettsted, tuftet på den rimelige elektriske kraften man fikk fra Daleelven.
Den første industrielle revolusjonen kom hit på slutten av 1870-tallet da hjørnestensbedriften Dale Fabrikker ble etablert. Nå har en ny industriell revolusjon feid over tettstedet.
Alt foregår inne i fabrikkbygningene til Rolf Hagebø, og man blir fort imponert straks man går inn.
Det ble i høyeste grad også næringsminister Monica Mæland som var til stede under den offisielle innvielsen den 9. februar av den nå høyt automatiserte virksomheten til Pallegrossisten. Hele 34 millioner kroner har det kostet, et imponerende høyt beløp tatt i betraktning av selskapet i fjor omsatte for i underkant av 30 millioner kroner. Investeringen kommer både Dalesamfunnet og familien til gode.
– Jeg kunne ha dyttet en masse penger i egen lomme, men det ville ikke ha gitt meg noen glede, sier Hagebø. – Nå er målet mitt å gjøre den så konkurransedyktig som mulig og at jeg etter hvert kan overlevere til familien. Da vil jeg trygge arbeidsplasser for både barn og barnebarn, legger han til.
Gründer på mange områder
Rolf Hagebø har mange jern i ilden og alle de ulike virksomhetene har han startet fra scratch.
Hemmeligheten for å lykkes er ifølge ham selv å kunne se muligheter, ha evnen til å være tålmodig og holde interessen oppe fra ideen er fanget til virksomheten er oppe og står, vilje til å stå på, være økonomisk, utnytte ressursene og ikke minst yte maksimal personlig service. En god beskrivelse av en vestlandsgründer med andre ord, bortsett fra at han er svært lite glad i budsjetter og regnskaper.
Etter å ha vokst opp på Dale flyttet han og kona Sølvi til Osterøy for 40 år siden. Der startet han opp med transport, og på det meste hadde Rasken Transport 13 vogntog og egen terminal. Men da Hagebø etter hvert innså at han var i ferd med å jobbe livet av seg, valgte han å overlate den virksomheten til en slektning.
– Parallelt med driften av transportselskapet startet jeg også opp med paller. Det var to virksomheter som støttet hverandre på en veldig god måte. Resultatet var at jeg klarte å utnytte materiellet veldig bra og hadde nesten aldri tomme lass.
De første årene ble alt avfallet fra produksjon av paller og ulike typer spesialkasser brent. Men etter at flammene en gang kom ut av kontroll og truet både ham selv og bygningene hans på Osterøy, sa han til seg selv: aldri mer. I stedet begynte han å produsere vedbriketter og også denne virksomheten er nå blitt flyttet til Dale.
I over 20 år har han også vært involvert i produksjon og salg av bunader. Den virksomheten inkluderer en fabrikk med 75 ansatte i Ghana som står for den mest tidkrevende produksjonen av skjorter og forkle.
Flyttet fra Osterøy til Dale
For snaue ti år siden kjøpte han den gamle fabrikkbygningen til Dale Fabrikker som lenge hadde stått tom. Med den fikk han 11.000 kvm for 2,8 millioner kroner. En latterlig lav kvadratmeterpris, men så var da heller ikke bygningen optimal tatt i betraktning at arealet er fordelt over hele seks etasjer, hvorav flere med søyler. Den trigget imidlertid noen gamle følelser hos Rolf.
– Ja, det var ett eller annet. Det var uansett en merkelig følelse å kjøpe denne bygningen som på det meste var arbeidsplassen til 1.200 personer og hvor både mine foreldre, svigerforeldre og en rekke gamle kjente hadde gått i gangene.
Men han stoppet ikke med den.
– En tilstøtende bygning på 5.000 kvm var også til salgs, og den måtte jeg betale fem millioner for, sier Rolf og ler. – Men med den fikk jeg blant annet rampe og annet jeg trengte, legger han til.
Ble bitt av automatiseringsbasillen
I en overgangsfase hadde Rolf produksjon både i de to fabrikkene han hadde på Osterøy og i de nyervervede lokalene i Dale, men etter hvert ble alt samlet på ett sted. I flere år foregikk både produksjonen av engangspaller og spesialpaller og -kasser, i tillegg til sortering, reparasjon og lagring av EUR-paller helt manuelt.
– Jeg hverken snakker med konkurrenter eller studerer hva de gjør og har alltid gått mine egne veier. Jeg har imidlertid alltid vært opptatt av kostnader og at det vi gjør skal skje raskt og effektivt, sier Rolf, som alltid har vært fascinert av automatisering og som for alvor fikk opp øynene for dette i fjor.
Etter å ha vært en trofast bruker av Toyota- og BT-trucker i nær en mannsalder fikk han kontakt med avdelingen for Logistic Solutions i Toyota Material Handling Norway for å kartlegge muligheten til å ta i bruk autotrucker i forbindelse med inn- og utlagring av EUR-paller i to etasjer. Avdelingens prosjektleder Vidar Nordby forteller at han og salgsansvarlig Jonny Tjøstheim raskt tok turen over fjellet og målte opp de to etasjene for å finne frem til en løsning. Etter hvert jobbet de også nært med ITO Intern Transport som Rolf hadde engasjert for den øvrige internlogistikken, inkludert automatisk flyt av paller gjennom både sortering og lagring.
Rolf forteller at Tjøstheim og Nordby raskt kom frem til en løsning for autotruckene som skulle gå i femte og sjette etasje. Totalprosjektet tok lengre tid enn han trodde, men tatt i betraktning av størrelsen og ikke minst kompleksiteten skulle det nær sagt bare mangle. Han forteller at det gikk tolv tegninger frem og tilbake med tilhørende diskusjoner og innspill fra både ITO og ham selv før de kom frem til et komplett anlegg som Rolf er svært godt fornøyd med.
– Jeg er veldig god til ikke å lage budsjett, sier Rolf med et smil. – Jeg har alltid en grunninnstilling om at dette skal jeg få til, og har en tendens til å skrive under kontrakter uten å ha snakket med banken på forhånd.
Det var for øvrig noe også næringsministeren kommenterte under åpningen og påpekte at det alltid er best å snakke med banken først.
– Ja da. Hun gjorde det. Da fikk jeg også høre av daglig leder Arne Hagen i ITO at de i begynnelsen var skeptiske til at en som jobbet med paller ville investere så mye, sier Rolf, som for øvrig var svært glad for støtten han fikk av Innovasjon Norge på 4,9 millioner kroner.
– Det krever mye arbeid og dokumentasjon for å overbevise Innovasjon Norge om at du har et godt nok prosjekt til at de støtter deg. Men de hadde troen på meg, og jeg har levert det jeg lovet. Alt i alt har jeg som nevnt investert 34 millioner kroner, men så har jeg da også fått et anlegg som ingen andre har og som ikke minst fungerer. Det er det viktigste.
Helautomatisk sortering og reparasjon
Rolf er synlig stolt når han viser oss rundt i området der to roboter som ble anskaffet fra Sverige står for det aller meste av produksjonen av nye engangspaller, spesialpaller, tre- og finérkasser.
Det omfattende ITO-anlegget starter ute ved rampen der dataene på innkjøpte EUR-paller først blir registrert på en computer før de deretter blir plassert på én av i alt fire parallelle baner som går inn i bygningen. Etter å ha gått gjennom en palleoppretter føres stablene videre frem til en robot fra ITO som tar én og én pall inn i en boks hvor de blir fotografert ovenfra av et vision-system levert av norske Tordivel. Deretter flytter roboten pallen over i en annen boks der den blir fotografert både under og på siden. Rolf kaller dette det usynlige øyet.
– Sekunder etter har systemet bestemt hvilken kvalitetsgruppe pallen tilhører, om den må repareres manuelt eller automatisk, eller om den er så dårlig at den går rett til brikettproduksjon samen med øvrig treavfall, forklarer Rolf.
Paller som skal lagres blir deretter plassert på en ny bane av en annen ITO-robot som enten plasserer 17 paller oppå hverandre eller fletter 25. Begge disse stablene er like høye og er tilpasset en standard lastbærer. Når stabelen er full skyves den over på en vogn som fører den til én av i alt 18 ventebaner.
Paller med skade blir plassert på en egen ventebane. De som må repareres manuelt blir plassert på et eget område for det, mens paller som kan repareres automatisk går først via en reparasjonsrobot som fjerner ødelagte komponenter før en annen setter nye på plass.
– Alt dette skjer helt automatisk, forklarer Rolf. – Alle pallene har en identitet og systemet husker ikke bare hvor den er plassert, men også hva som må gjøres med den, enten det er snakk om å erstatte en kloss eller et ødelagt bord.
Midt i produksjonslokalet har de bygget opp et kontrolltårn der Rolfs bror Kåre har full oversikt over de mange forskjellige datasystemene som gjør denne automatiske flyten mulig. Herfra styres også inn- og utlagringen fra de to lageretasjene.
Paller som skal til innlagring føres over på en av de to utbanene som går parallelt med dem som går inn. Ved enden av disse går de over en bro på noen få meter som senkes ned og over på en ny bane som fører pallestablene gjennom en tunnel og frem til en heis som tar dem videre oppover i etasjene til autotruckene. Her holder de orden på ca. 20.000 paller av forskjellige kvaliteter i hver etasje. Datasystemet viser hva som til enhver tid er på lager.
Standard BT Autopilot
Vidar Nordby forteller at de to autotruckene er av typen BT Autopilot med modellbenevnelse SAE 160. De er basert på standardprodukter og produseres i Sverige. Begge har en løftekapasitet på 1.600 kilo og en løftehøyde på 2.350 mm. Hos Pallegrossisten løftes imidlertid pallestablene bare så vidt klar av bakken.
– Autotruckene er laserstyrt og etter å ha målt opp bygget og laget en bakgrunnstegning monterte vi en rekke reflektorer på veggene. Etter å ha kjørt en referanserunde med autotruckene i hver etasje for å lese inn refleksene har vi oppnådd en nøyaktighet på pluss minus 10 millimeter i hele bygget. Det gjelder også i femte etasje hvor det er en rekke søyler, og det er derfor et godt bevis på at slike ikke er noen begrensning for våre autotrucker, sier Vidar, som opplyser at navigasjonssystemet hele tiden mottar signaler fra fire reflektorer. Han legger til at det er svært enkelt å endre layouten hvis det skulle være behov for det.
Sikkerhet står naturligvis i høysetet og foran på autotrucken er det en Sick lasersensor med dynamiske felter som justerer lengden og vinklene etter kjørehastigheten som er optimalisert for høyest mulig effektivitet.
– Bakover, altså i palleretningen, er hastigheten begrenset uten sikkerhetssensor, men siden Pallegrossisten også valgte å montere en tilsvarende sensor under gaffelvognen kan hastigheten optimaliseres og økes også i den retningen. Det bidrar naturligvis til å effektivisere trucken i stor grad, sier Vidar. – Den sensoren støtter også navigasjonssystemet med å gjenkjenne en pall når gaflene nærmer seg en slik. Deretter tar sensorene som er montert på en hengslet plate ytterst på gaflene over. De peker både oppover og fremover og hvis platen skyves til side stanser trucken.
Et siste sikkerhetselement er sensorer som også dekker hver side av autotrucken, og straks man tar tak i ledehendelen blir den som en helt konvensjonell manuell truck.
Får tildelt lokasjon fra kontrolltårnet
Oppgaven til de to truckene er å hente eller bringe pallestabler til og fra heis. Toyota Storage Planner er et brukergrensesnitt mot ITO-systemet og det gir Kåre i tårnet et godt oversiktsbilde av lageret.
Når noe skal lagres inn, taster han inn artikkelnummer og antall og deretter reserveres lokasjon som truckene deretter leverer til.
Motsatt vei lyser Toyota Storage Planner opp de aktuelle radene når artikkelnummer og antall tastes inn, og truckene begynner å hente når han gir beskjed om det.
Full oversikt
Rolf forteller at virksomheten hans i Dale nå er blitt så fullautomatisert at svært mye kan gå av seg selv – også på natten. Selv er han bare innom fabrikken et par ganger i måneden og holder seg primært på kontoret han har beholdt på Osterøy.
Etter å ha fått montert opp ikke mindre enn 26 kameraer i fabrikken man full kontroll fra kontrolltårnet. Derfra kan både han og Kåre enkelt se hvis det skulle være noen utfordringer. Det hender også at de ber meg ta en titt hvis de er usikre på noe og foreslå hva de skal gjøre. Det er rett og slett et godt hjelpemiddel, sier Rolf.
Vinner på personlig service
Rolf vektlegger at Pallegrossisten alltid skal kunne hjelpe kundene, enten det er forespørsler om EUR-paller, spesialpaller, spesialkasser eller for den saks skyld paller i plast, aluminium eller stål som han også formidler.
Til tross for den høye automatiseringsgraden er han ikke interessert i volum.
– Vi har ikke lagt opp til å kunne spy ut 10.000 paller om gangen, sier han.
Spørsmålet over hvor mange han selger blir blankt ignorert. Det er som å spørre en same om hvor mange rein han har.
– Nei, her går det veldig mye i spesialtilpasninger og skreddersøm. Ingenting er problem – kun en utfordring, sier Rolf, som også legger sin ære i å yte god gammeldags personlig service.
Han forteller at mange av kundene velger å ringe inn forespørsler og bestillinger fordi de setter pris på å snakke med noen og på den måten får en personlig service.
– Vi får også mange slike henvendelser på mail, men jeg liker ikke å svare på den måten. I stedet foretrekker jeg å ringe dem tilbake. På den måten får man mye bedre kontakt med de kundene som også får følelsen av at vi bryr oss om dem. Strengt tatt behøver jeg nesten ikke svare, for som regel sender vi ut varen samme eller neste dag. Jeg kan i hvert fall ikke huske sist vi hadde en delleveranse.
Resultatet er svært gode tilbakemeldinger fra så vel små som store selskaper. Palegrossisten bygger blant annet mange trekasser og spesialpaller for Rolls-Royce i tillegg til flere andre større og mindre kunder.
Den høye servicegraden kommer raskt til kjenne under intervjuet som til stadighet blir avbrutt av at mobilene ringer.
– Beklager, jeg må bare ta den.
– Selvfølgelig, svarer vi.
– Det var en kunde oppe i Tromsø som ønsket 1.000 paller. En relativt god ordre, sier Rolf. – Bare vent litt til er du snill. Jeg må bare hjelpe dem med transporten også.
Ny telefon. Og en til.
– De fleste kundene velger å la meg ordne transportene fordi de vet at de får det billigere på den måten. Da blir de lojale vet du. Sikkert fordi jeg selv har jobbet i bransjen og vet hvem jeg skal snakke med.
Selv disponerer han en 12-tonns skapbil som brukes i nærmiljøet og den utnyttes selvfølgelig optimalt.
– For resten av landet bruker jeg hovedsakelig Tollpost, sier Rolf, som ikke liker å si PostNord når vi minner ham om navneskiftet for et par år siden. – Men de er veldig flinke de i Bergen, legger han til.
Stopper ikke med dette
Rolf unngår naturligvis ikke også å nevne at Pallegrossisten tar kvalitet og miljøansvar på alvor og arbeider etter de sist reviderte ISO-9001:2015 og ISO-14001:2015-normene.
Med automatisering sier det seg selv at virksomheten etter hvert skal få gevinster.
– Jeg ser at jeg selger, klarer å betale regningene og at jeg har penger i banken. Det holder for meg.
– Etter å ha fortalt hvor mye både familien og lokalsamfunnet betyr for deg er det jo tydelig at du er en person med et stort sosialt ansvar. Har du noen etiske problemer med at automatisering ofte medfører færre arbeidsplasser?
– Nei, og det blir det heller ikke. Her har jeg i dag åtte ansatte i tillegg til de tre på kontoret og kona som fører regnskap. Hvis jeg hadde villet, ville jeg klart meg med fem på fabrikken.
Etter å ha vært særdeles aktiv overfor Innovasjon Norge i forbindelse med prosjektet som nå er kommet 99 prosent i mål, lovet Rolf dem at han skulle være rolig et års tid.
– Men det gikk bare én måned før jeg banket på døren til dem på nytt. Nå har jeg fått klarsignal på at Innovasjon Norge vil bidra med både tilskudd og lån til et nytt prosjekt på syv millioner kroner som jeg har på trappene, sier Rolf, som nå planlegger å automatisere lageret i ytterligere en etasje. Mesteparten av pengene skal imidlertid benyttes til å etablere egenproduksjon av pallekarmer.
– Også den produksjonen vil bli helautomatisert. Etter å ha lagt inn materialer i den ene enden vil det komme ferdige pallekarmer ut i den andre enden – ferdig stroppet på pall.
Ja da, jeg innrømmer at jeg er bitt av automatiseringsbasillen, sier Rolf. – Og nei, jeg har ikke snakket med banken ennå. Det er ikke så enkelt å skaffe nye millioner, men jeg er ikke i tvil om at jeg får med meg banken. Selv om jeg er litt annerledes enn mange andre, vet de at jeg alltid klarer å levere gode resultater og da smiler banken tilbake til meg, avslutter Rolf Hagebø.
Industri 4.0 Industri 4.0 er opprinnelig et strategisk initiativ fra tyske myndigheter for at landet skal ta en ledende rolle innenfor industriell IT. Basis er full digitalisering i smarte fabrikker der alt er koblet opp mot hverandre. Industrie 4.0 benevnes ofte som den fjerde industrielle revolusjon da den etterfølger den tredje (automasjon gjennom it og elektronikk), den andre (elektrifisering og masseproduksjon) og den første industrielle revolusjon (mekanisering med vannkraft og damp). Smart utnyttelse av Industrie 4.0-teknologier i logistikken var blant hovedtemaene på den store logistikkutstillingen CeMAT som nylig ble avholdt i Hannover. |